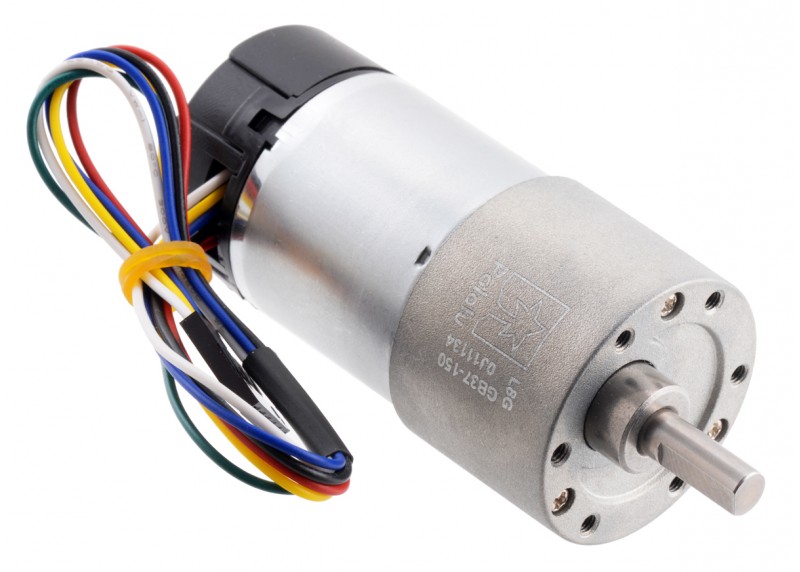
Motor de CC con tacómetro
Una de las necesidades de un sistema impulsado por un motor de corriente continua es que su velocidad se pueda mantener constante, ya que en la mayoría de las aplicaciones de servomecanismos la velocidad de giro debe ser conocida y plausible de ser controlada desde un circuito de comando.
Como esta característica no es propia de los motores de corriente continua, que cambian su velocidad según la carga mecánica que tienen aplicada, se necesita utilizar un sistema de medición cuya salida de señal, realimentada en el circuito de manejo de potencia, sea proporcional a la velocidad.
Al efecto se utiliza un tacómetro, que es un artefacto que debe generar una señal proporcional a la velocidad real del motor con la máxima precisión posible.
Si se aplica una carga mecánica al eje del motor de corriente continua y la velocidad disminuye, esta disminución se refleja en la señal del tacómetro. Como la señal es ingresada al circuito de control de velocidad del motor, con la configuración apropiada en este circuito de realimentación negativa se reajusta la corriente alimentada al motor hasta llevar la velocidad de nuevo al valor deseado.
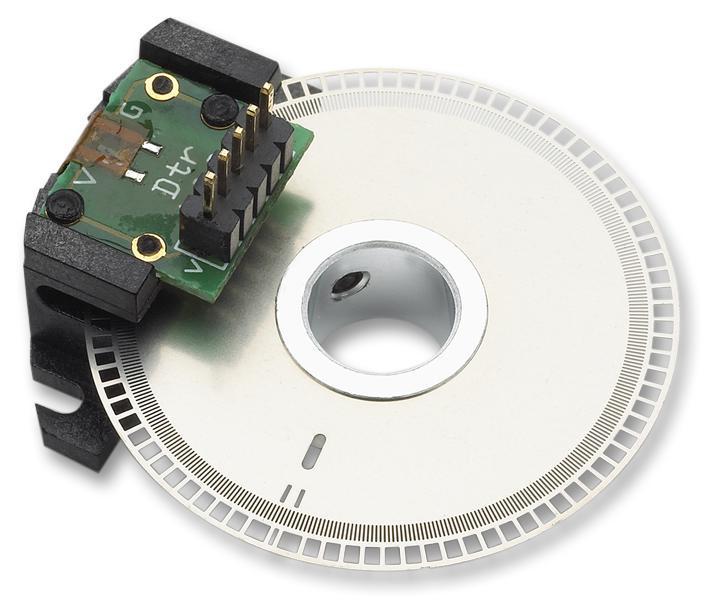
Disco de encoder
El tacómetro puede ser un generador de CC adosado al mismo eje, y por lo general integrado en la misma carcasa con el motor, o también un disco con ranuras o franjas alternadas de color claro y oscuro, con un sistema óptico de lectura que entrega pulsos al enfrentarse las ranuras o bandas sobre un fotosensor.
También existen tacómetros (de concepto similar al de bandas o ranuras) que utilizan un sensor magnético (pickup magnético) que detecta el paso de dientes metálicos por delante de él.
La señal analógica del tacómetro generador de CC es introducida al circuito por medio de amplificadores operacionales, mientras que la señal del tacómetro de bandas o ranuras, que básicamente es un pulso, debe ser procesada digitalmente.
MOTOR DE CORRIENTE CONTINUA CON TACÓMETRO

Tacómetro:
1. Tapa posterior | 2. Cojinete de bronce | 3. Carcasa | 4. Imán | 5. Cilindro de acople | 6. Bobina | 7. Conmutador | 8. Porta escobillas
Motor CC:
9. Escobillas | 10. Conmutador | 11. Bobina con eje | 12. Eje | 13. Carcasa | 14. Cojinete | 15. Retén | 16. Cables de conexión
Los tacómetros de pulsos (a los que también se les llama «encoders«), si bien requieren mayor procesamiento de señal para realizar la realimentación, ofrecen la ventaja adicional de que se pueden contar digitalmente los pulsos y así saber con precisión la cantidad de vueltas y fracciones de vuelta que ha completado el sistema.
MOTOR DE CORRIENTE CONTINUA CON ENCODER DE RANURAS
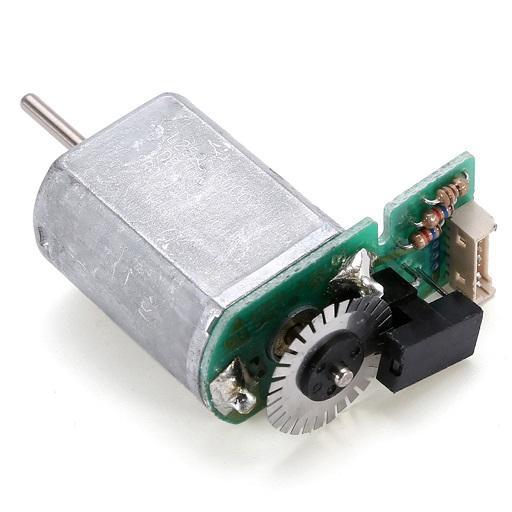
Además de encoder, existe un detector llamado resolver. Un resolver es un sensor formado de un par de bobinas que se excitan con una señal externa. Las bobinas están colocadas en posiciones ubicadas 90° entre sí, de modo que, según su orientación, captan con distinta intensidad la señal de corriente alterna (CA).

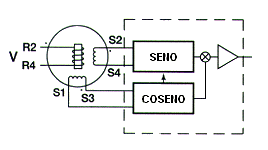
Esta configuración da como resultado salidas seno y coseno que tienen una relación con el ángulo en que está el eje de rotación del resolver con respecto a la señal de CA. El procesamiento del seno/coseno da como resultado la posición angular del sensor. Este tipo de sensor ofrece gran precisión y se sigue utilizando cuando se necesita determinar la posición absoluta de un eje.
DIAGRAMA DE LA REALIMENTACIÓN CON TACÓMETRO Y ENCODER/RESOLVER
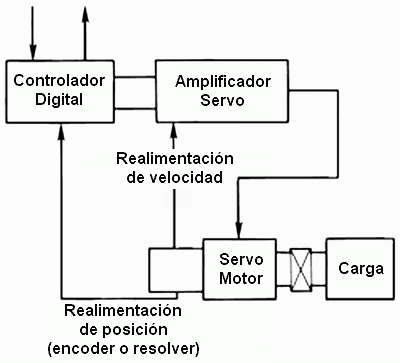